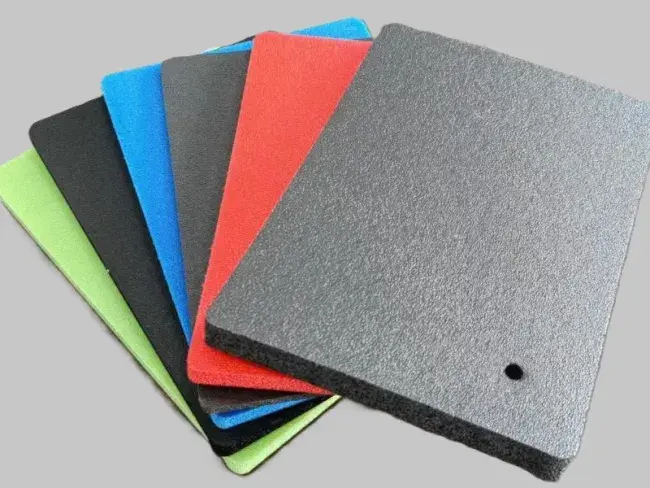
Specification
- Foaming times: 3-40 times
- Width: 500-1800mm
- Thickness: single layer 2-12mm; multi-layer 12-200mm
- Surface treatment: calendaring or corona treatment is available.
- Colour: black, white, grey, colourful, etc., can be customized.
XPE foam, known as Cross-Linked Polyethylene Foam, is a high performance closed cell foam. It is made by chemical cross-linking or radiation cross-linking and has excellent physical and chemical properties.
Features
- Light weight and high strength
- XPE foam is low density and lightweight, but has high compressive and tear strength.
- Suitable for applications that require weight reduction but still need to maintain a certain level of strength.
- Excellent thermal and acoustic insulation.
- Due to its closed cell structure, XPE foam has excellent thermal and acoustic insulation.
- It is widely used in building thermal insulation, automobile sound insulation and other fields.
- Water and chemical resistance
- XPE foam is not easy to absorb water, even if it is soaked in water for a long time, it can maintain its original physical properties.
- It has good resistance to most chemicals and is suitable for packaging and protection in chemical environments.
- Environmentally friendly and non-toxic
- No harmful substances are used in the production process, and the finished product does not contain any toxic ingredients.
- It is recyclable and meets modern environmental requirements.
- Easy to process
- XPE foam can be processed by thermoforming, cutting and other methods, which makes it easy to be customised into different shapes.
- The surface is smooth and even, easy to adhesive, printing and other secondary processing.
Application
- Packaging industry
- As a cushioning material to protect fragile items from damage during transport.
- Used for lining packaging of high-end goods such as electronic products and glass products.
- Construction industry
- Used as thermal insulation for walls and roofs to improve the energy efficiency of buildings.
- Used as an underfloor matting layer to provide comfortable footing and reduce noise transmission.
- Automotive industry
- Used as acoustic insulation in automotive interiors to reduce interior noise levels.
- Used in seat padding to increase ride comfort.
- Sports & Leisure
- To make yoga mats, fitness mats and other sporting goods, providing good support and non-slip properties.
- Used as core material for outdoor activities equipment such as water flotation boards and life jackets.
- Healthcare
- Used to make wheelchair cushions, mattresses and other medical equipment, providing a soft and supportive surface.
- Used as a base material for medical supplies such as disposable surgical sheets and dressing backings.